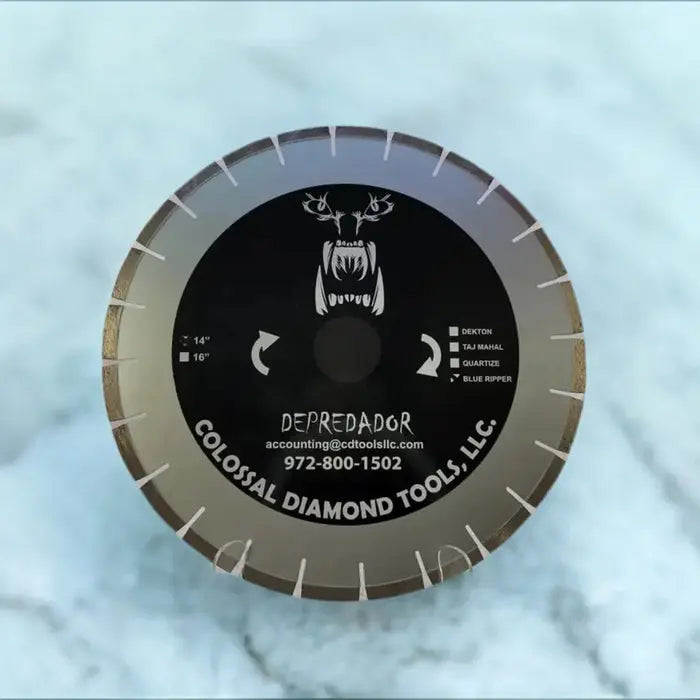
Precision Cutting Blades: Industrial Materials Cutting is the very root of all perfection no doubt about it.
Precision Cutting Blades
Precision is the greatest weapon in the industry of manufacturing. From metal-using materials to plastics, encapsulating components to assembling components, a clean cut is very important. There is no doubt that it plays a huge role in coming up with high-quality assemblies or components. So this is where a sharp, precision knife holds the position. Specially meant to get the work that cannot be replicated by any other tools, this equipment is accepted as very critical in different industries, for example, aerospace, automotive, woodworking, and so on, and electronics. This article discusses precision-cutting blades, their characteristics, areas of use, and how they are cut on a fine scale. It talks about the painstaking processes that are used in their creation.
Understanding Precision Cutting Blades
Colossal Diamond Tools are cutting tools that are well known for their exceptional sharpening, durability, and capability to provide precise cuts with minimal irregularities. For the blades, the expected level of accuracy is as high as possible, and they must be reliable without any kind of random issue. As in the case of other traditional cutting tools, however, precision cutting blades do rely on advanced materials, coatings, and design elements, which help in the improvement of their cutting capability and prolong the tool’s life.
Materials and construction
Firstly, the quality resources that are employed during the manufacturing of precision cutting blades prove to be quite important. High-quality steels, such as HSS or W2, are, for instance, the most commonly selected base materials because of their strength and resistance to wear. These alloys are precisely composed of a mixture of various components, like vanadium, cobalt, or chromium, which enhance their hardness, toughness, and temper resistance.
Besides the base material, blades produced by Precision Cutting are additionally coated with special coatings, which help to improve their performance. These coatings, which are made of materials such as titanium nitride (TiN), aluminum titanium nitride (AlTiN), and diamond-like carbon (DLC), not only give the blade good lubricity, wear resistance, and better heat handling, which allows them to maintain sharpness and edge for longer periods,.
A precision slitting die can be made in different options of shapes and sizes, as the application dictates. Common blade shapes may include circular sawblades, band sawblades, and router bits, as well as jigsaws and hobby knives. Each pattern is still being designed in a very detailed way to make cuts more effective, reduce vibration, and create fewer burrs.
Precise Vector Cutter Clinical Examples
The multi-dimension influence of precision cutting blades is tremendously wide across a wide river of industries where high result accuracy is required. Here are some of the key areas where these cutting tools excel:
Woodworking and Cabinetry: The woodworking industry's precision cutting blades are utilized for cutting intricate patterns, opening up exact joints, and performing, much in that manner, the smooth and flawless work on the wood products.
Electronics and Semiconductor Manufacturing: The manufacture of printed circuit boards, computer elements, and other electronic devices are the very things for which a precision cutting blade is generally utilized for a precise cut on fragile materials.
Medical Device Manufacturing: Medical implant production, surgical instrument manufacturing, and other medical apparatus implementation processes are the domain of precision cutting blades, which take on the responsibility of dimensional accuracy and surface finish, which are very significant issues with patient safety and device performance.
Metalworking and Fabrication: From the machining process to the making of highly ornate metal art pieces, precision cutting blades serve as fundamental productivity enhancers in the metalwork industry.
The characteristics of advanced cutting blade precision are defined next.
Previewed cutting knives have many more benefits than standard cutting tools, so they have become a favorite in many applications requiring accuracy. Here are some of the key features and benefits:
Exceptional Cutting Accuracy: Precision Cutting Blades Engineered to give maximum precision in cutting even with less deviation and ensure a consistent and similar result.
Longer Tool Life: The super materials, coatings, and construction elements used in cutting blades see repetitive use cases, which, in the context of that, improves the downtime and the cost of replacing them.
Improved Surface Finish: The precision cutting blades with unique sharpness and edge quality give the buyers much smoother finishes, thereby cutting down the other finishing extent.
Reduced Burr Formation: The precision geometry and guided cutting edge of such knives are designed to guarantee the least deformed ends plus fewer burrs, as a result of which neat cuts are formed and the additional processing is done less often.
Increased Productivity: With quicker cutting speeds, minimized vibrations, and extended tool life, precision cutting blades play a vital role in manufacturing processes that aim for improved productivity and will reduce the amount of time spent in these operations.
Effective Utilization and Maintaining the Accuracy of Precision Cutting Tools and Knives
Ensuring the appropriate use and maintenance procedures is vital for the optimal yield and durability of precision-cutting blades. Here are some key considerations:
Workpiece Preparation: Secure that the workpiece is firmly pinned and supported and that particle displacement and vibration are reduced during cutting operations.
Cutting Parameters: Follow the speed, feed rate, and depth of cut values recommended for the material and blade by the manufacturer’s instructions.
Coolant and Lubrication: Ensure to use the coolant or lubricant specified for a given cutting operation, as it helps in reducing the tool-heat buildup that slows down cutting speed and reduces blade life.
Blade Storage and Handling: Shelves up to the CNC precision cutting blades in a place that is protected from rain, dust, and other pollutants. Manage them appropriately since carelessness can cause the cutting edges to be damaged.
Regular Inspection and Maintenance: Check for sharpness and indicate blade wear, chipping, or damage. Make sure you replace blades when necessary to maintain the quality of the cut. Conduct daily maintenance and implement cleaning and sharpening to ensure smooth running.
Conclusion
Precision cutting blades are core instruments in the industrial community nowadays and contribute to manufacturing's unmatched joining accuracy, surface finish, and productivity. Utilizing sophisticated materials and coatings, as well as their exceptional precision engineering, these tools have been driving productivity in many sectors like aerospace, automotive, woodworking, and the medical device industry, to mention a few.
With the development of technology, the demand for making precision-cutting blades can be increased, and thereby progress could be made in material science, blade shape, and production steps. Such innovative tools can indeed be a great tool for manufacturers in any industry if they have sufficient investment in them and simultaneously deploy proper usage and maintenance practices. This can even improve productivity, quality, and so on.
FAQs
Why are precision-cutting blades preferable to regular cutting tools in terms of their main advantages?
Precision cutting blades deliver exceptional cutting dimensions, prolonged tool life, a smooth finish, weaken burr development, and offer improved production.
What materials are the most widely used in precision engineering?
High-performance steels like HSS (high-speed steel) or tungsten carbide are the materials commonly used as the substrate, often hardened or surrounding the material with elements such as vanadium, cobalt, or chromium for better properties. Titanium nitride (TiN) or aluminum-titanium nitride (AlTiN) coatings are also used to achieve enhanced performance. The diamond-like carbon (DLC) coating is another added advantage of these machines.